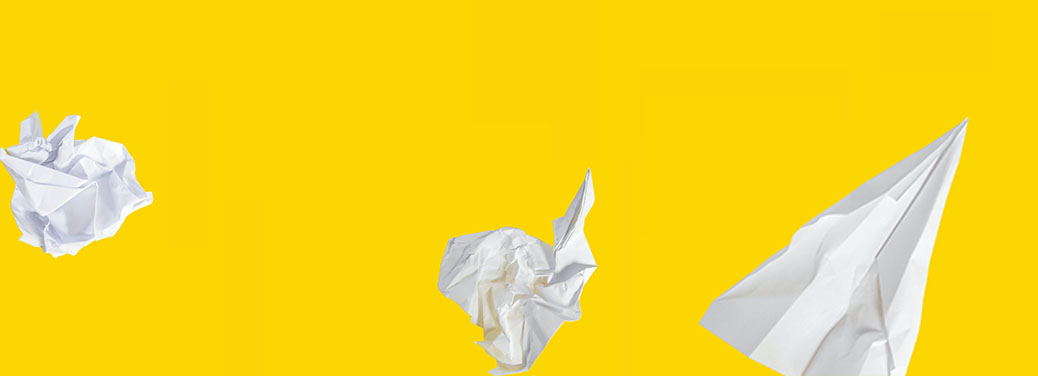
Jak powstaje papier
W jaki sposób powstaje współczesny papier? Proces produkcji papieru jest równie fascynujący, co skomplikowany. Niestety - nie unikniemy uproszczeń i skrótów. Jednak dzięki temu łatwiej będzie zrozumieć, jak pień drzewa przetworzony do postaci płynnej zamienia się w kartkę papieru. Brzmi jak magia, ale to tylko kwestia odpowiedniej technologii. Poznaj etapy produkcji papieru.
Skąd wziąć drewno?
Odpowiedź jest oczywista – drewno bierze się z lasów. Według Lasów Państwowych drewno, które trafia do papierni, pochodzi z cięć pielęgnacyjnych. Przerzedzane są młode lasy (tzw. młodniki), by dać więcej miejsca na rozwój drzewom silniejszym. Następnie wycięte drzewa trafiają do miejsca, w którym wytwarza się papier, czyli do papierni. Jednak do wytworzenia papieru potrzebne jest nie tyle drewno, co włókna celulozowe. (Tu trzeba wspomnieć, że w skład papieru wchodzą zarówno włókna roślinne z drzew, jak i inne dodatki, które wpływają na późniejsze właściwości papieru.)
Metody pozyskiwania włókien celulozowych
Metoda chemiczna
Przy tej metodzie drewno zostaje najpierw zmielone na zrębki, które są poddane dalszej obróbce chemicznej – są trawione przez chemiczne dodatki. Dzięki temu otrzymujemy praktycznie całą zawartą w nim celulozę, bez niepożądanych innych składników. Taka masa nazywana jest więc “masą bezdrzewną”. Warto wspomnieć, że jeśli spotkaliście się z określeniem “papier bezdrzewny” nie oznacza ono wcale, że do jego produkcji nie zostało wykorzystane drzewo. Po prostu w jego składzie poza celulozą mogą znajdować się jedynie niewielkie ilości składników pochodzących z drewna. Włókna otrzymane metodą chemiczną są długie, o wysokiej wytrzymałości i odporne na starzenie się. Ciekawe jest, co się dzieje z pozostałymi składnikami drewna. Wszak celuloza stanowi mniej więcej połowę jego zawartości. Co z resztą? Wykorzystuje się ją jako surowiec bądź źródło energii. Dzięki temu nowoczesne papiernie są często samowystarczalne energetycznie.
Metoda mechaniczna
W tej metodzie drewno jest mielone aż do momentu oddzielania się włókien celulozy. W przeciwieństwie do metody chemicznej, do produkcji papieru poza celulozą wykorzystuje się również inne substancje drzewne np. ligninę i żywice. Użyte zostaje praktycznie 95% objętości drewna. Włókna uzyskane w tym procesie mają nieco inne właściwości niż te pozyskiwane chemicznie, co wpływa na rodzaj papieru, który powstaje.
Oczywiście nie są to jedyne metody pozyskiwania włókien. Istnieje wiele ich rodzajów, a także metod łączących w sobie cechy obu wyżej wymienionych np. chemotermomechaniczna. Dziś jednak nie będziemy się na nich skupiać.
Masa papiernicza
Papier wytwarza się z tzw. masy papierniczej. Kluczową kwestią na tym etapie produkcji jest odpowiednie przygotowanie włókien celulozy, ponieważ wpływa to na wiele właściwości papieru, który zostanie z tej masy wytworzony. Włókna zostają zmielone, dzięki temu stają się bardziej giętkie i elastyczne. Masa papiernicza nie składa się jednak tylko z włókien. Zawiera 99% wody. Poza tym znajduje się w niej zazwyczaj klej papierniczy, węglan wapnia i barwniki. Proces powstawania papieru opiera się na dokładnym kontrolowaniu tych składników, ponieważ właściwości papieru zależą od ich proporcji. Gdy masa jest już gotowa, trafia do maszyny papierniczej.
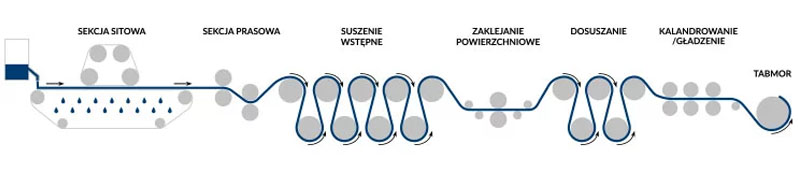
Na zdjęciach „Schemat produkcji papieru”.
Maszyna papiernicza
Skoro masa papiernicza jest właściwie płynem, to w dużym uproszczeniu można powiedzieć, że głównym zadaniem maszyny papierniczej jest jej odwodnienie. Od momentu wlania mieszanki do maszyny poprzez wlew, aż do momentu uformowania papieru, masa będzie suszona kilkukrotnie, na różnych etapach. Jak możecie wiedzieć z tekstu “Z czego składa się papier?”, nawet gotowe arkusze nie są w pełni pozbawione wody. W zależności od rodzaju papieru woda może stanowić od 3 do 7% jego masy.
Gabaryty maszyn papierniczych są imponujące – mogą mieć do 150 m długości i 11 szerokości. Jeszcze większe wrażenie robi czas, jaki zajmuje przekształcenie masy na gotowy papier. Zajmuje to od 10 do 30 sekund! Prędkość, z jaką wstęga porusza się w maszynie, może osiągnąć nawet powyżej 2000 m/min.
Masę wlewa się przez wcześniej wspomniany wlew, skąd trafia na sito. Tam z pomocą elementów odwadniających i próżni pozbawia się ją znacznej części wody. Kolejnym krokiem jest prasowanie masy za pomocą cylindrów i filców. Nacisk na spilśniającą się masę sprawia, że traci dalszą część wody. Ten etap wpływa na sztywność, wytrzymałość, nieprzezroczystość i ostateczny wolumen papieru. Następnie wstęga przepuszczana jest przez ciąg stalowych cylindrów i ogrzewa się ją parą o temperaturze 120 stopni Celsjusza. Tu odbywa się suszenie wstępne. To bardzo ważny etap, ponieważ masa została pozbawiona wody na tyle, że można nazwać ją papierem. Potem następuje zaklejanie powierzchniowe. Polega na pokrywaniu powierzchni wstęgi papieru cienką warstwą skrobi. Dzięki temu zabiegowi papier jest bardziej trwały, odporniejszy na ścieranie, ma lepsze właściwości drukowe i nie pyli się. W zależności od rodzaju papieru, w kolejnym etapie jest on gładzony przez maszynowe gładziki lub kalandrowany, czyli nadawana jest mu ostateczna grubość. Następnie jest nawijany na zwój zwany tamborem. Na końcu jest cięty na arkusze bądź mniejsze zwoje. Teraz papier jest gotowy do dystrybucji.
W takiej formie papier trafia do drukarni, gdzie ma szerokie zastosowanie i staje się surowcem do tworzenia książek, gazet, opakowań czy innych wyrobów papierowych. Teraz nic nie stoi na przeszkodzie, aby poddać go procesowi druku.
Współczesna produkcja papieru drukowego - podsumowanie
Papier drukowy, używany na co dzień do tworzenia książek, gazet i innych wyrobów z papieru, powstaje w wyniku zaawansowanego procesu technologicznego. Masa włóknista wzbogacona dodatkiem innych rodzajów włókien oraz wypełniaczy organicznych cechuje się dużą wytrzymałością i wieloletnią trwałością. Wypełniacze te wpływają na jakość druku oraz trwałość papieru. Współczesna produkcja papieru uwzględnia również środki zaklejające, które nadają papierowi odpowiednią gładkość i odporność na wilgoć, co jest istotne, np. w produkcji ważnych dokumentów (m.in. produkcji banknotów) czy innych specjalnych zastosowań.