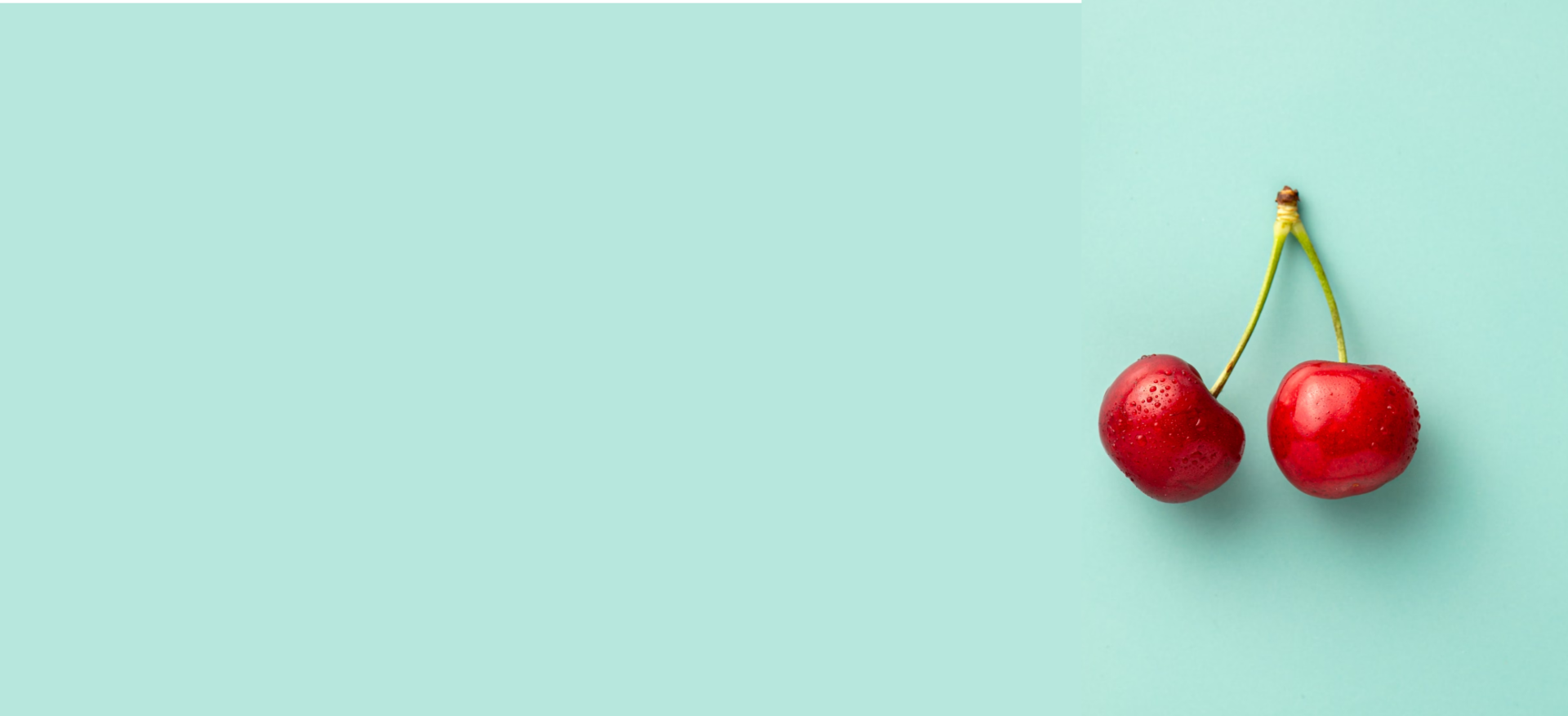
Basic quality standards
This procedure sets out the quality standards applied by Totem.com.pl digital printing house and outlines any deviations permitted due to technical limitations. These limitations arise from the quality of materials used in the production and technological constraints inherent in the machines used to produce an order.
1. General quality standards
Digital printing technology guarantees the highest quality of colour reproduction, however, some defects might are likely to occur.
a. Inkjet printing
- minor imperfections may occur in the form of streaks/lines resulting from automatic compensation caused by temporary clogging of the print head. The resultant marks would be noticeable on sections of the print where dark, highly-saturated colours are used, in particular on large-format photographs and colour backgrounds fully covered with ink (solids),
- minor imperfections may occur in the form of white lines called “missing nozzles” resulting from print head clogging,
- the above imperfections may occur in particular when printing on coated substrates.
b. Electrophotographic printing
- glossiness of the print,
- possible uneven coverage and minor discoloration where solid colour is applied,
- the above imperfections may occur in particular when printing on coated substrates.
2. Printing
A colour proof may be provided to enable production of a print copy consistent with it. Colour proofs submitted for printing must be uniform. If proofs are submitted with, for instance, a sheet from a previous print (print sheet without additional enhancements), the Client has to specify which of the provided proofs is the valid one.
In the absence of Client’s guidelines regarding the colours the printing process is carried out on the basis of a preview of the graphics on a specialized colour test monitor, based on the applicable ISO standard. Where the RGB colour space is used in production files, the colour of the print may differ significantly from the file / preview / template submitted for printing.
Due to the specific nature of the digital printing process, it may be accompanied by the occurrence of cockling, which might sometimes result in warped pages.
2.1. Proofs
A proof submitted for printing as the effective colour proof should be produced in accordance with ISO 12647-7 and provided with a certificate. If there isn’t one, a printout can be used as a print proof, however colour discrepancies between the finished product and the proof should be expected to occur.
The following details should be shown on the proof:
- date on which it was produced,
- project title/order number,
- UGRA-FOGRA media wedge,
- measurement compliance with the applicable standard.
2.2. Print sheets from previous print runs
A print sheet from a previous print run, which has not been subjected to additional enhancement processes (UV varnish, glossy/matte/soft-touch foils) can also be used as a print proof. The order from which the sheet originates should not be older than from the past six months, and the sheet itself must not have been exposed to direct sunlight. The substrate of the sheet provided as a colour proof should be consistent with the material to be used for printing the current order. This is crucial in terms of correctness of the white colour.
2.3. Client’s approval of a print at the press
In the event that the Client approves a print directly at the printing press, the Client is obliged to sign the sheets that automatically become a proof for printing. The print run is then produced using that proof.
2.4. Printing without a colour proof or approval by the Client
Printing will be carried out in compliance with the applicable ISO standard. The colour of the print depends on the material chosen by the Client and the printing technology applied. If the white colour does not comply with the colour terms of reference as prescribed by the standard, it is possible that a discrepancy between the colours may occur. The colours of the finished product are also affected by additional enhancements such as:
- UV/dispersion varnishes,
- glossy/matte/soft-touch/textured foils.
Visual assessment is carried out in standardized D50 lighting consistent with the ISO standard. The printing of special colours is based on the Pantone colour chart. Due to the inability to perform an accurate colour density measurement, the colour is deemed to have been correctly printed when, during the visual assessment, it falls between the (+) proof and the (-) proof provided by the Client. Additional enhancements such as application of glossy/matte/soft-touch/textured foils or UV varnishes can cause the colour to change unpredictably, depending on the graphic elements of the printed product. Totem cannot be held responsible for any such changes in colour, as the changes occur beyond our control and cannot be measured in any way. In order to avoid undesirable changes in colour, certain tests are required that can be carried out at the Client’s express request and expense.
2.5. Colour registration
Permissible deviations in registration of successively printed colours as measured in the centre of the sheet:
- Acceptable <= 0,4 mm
- Not acceptable > 0,4 mm
3. Enhancements
3.1. Varnishing
Due to the possible paper cockling in digital printing, the expected varnishing standards sometimes might not be maintained. A UV varnish layer is considered faulty if there are any uncoated spots on the surface intended for varnishing.
The varnish layer should be applied evenly and without any gaps. The following differences in registration of the spot/raised (multi-level)/textured UV varnish applied with the image are permitted:
- Acceptable <= 1 mm
- Not acceptable > 1 mm
3.2. Stamping
Stamping should be as deep as practicable for a given material, but it should not cause the material to crack at the edges of the area worked. The stamping area should be flat, even and of uniform depth, and free from any physical damage.
In the case of embossing, debossing and hot foil stamping (MGI) the following tolerances in registration of the enhancement with the image:
- Acceptable <= 1 mm
- Not acceptable > 1 mm
3.3. Die-cutting
The guidelines for the layout of die-cut elements should be included in the order. An imposition can be provided as an additional model for die-cutting. The offset of an element to be cut should not exceed the permitted tolerance range.
Permitted tolerance:
- Acceptable <= 1 mm
- Not acceptable > 1 mm
3.4. Edge printing
We use inkjet technology for edge printing. Please note that besides all the benefits, there are certain disadvantages of the technology when applied to book edges. There is a risk of potential defects, such as the following:
- Some minor imperfections might appear in the form of dots or lines, resulting from automatic compensation if the printhead gets clogged. The effect can be perceptible in large format photos and areas covered by solid colours.
- Minor defects resulting from printhead clogging (having the effect of ‘missing nozzles’) can include some white lines; this happens particularly in the case of printing on coated materials.
- Gloss differential, uneven coverage or slight discolouration on surfaces with solid coverage might appear, especially when printing on coated materials.
Registration tolerance:
- ≤ 1 mm acceptable
- > 1 mm not acceptable
Other defects that might occur in edge printing:
- Where the book block has graphics in the bleed area, the edges might not be completely covered by ink.
- Where the book block is glued, the spine-side of the edge might not be covered by ink in the area where the glue has been applied, or the glue might show through (in perfect-bound softcovers and hardcovers).
- Where one or two edges are printed, some ink mist might appear on the adjacent unprinted edge(s).
- Where a text is printed on the edge, it might become displaced if the block thickness parameter is not maintained throughout the print run.
- When printing on book blocks with rounded corners, the graphics might become a little blurred on the rounding. There is also a risk of misregistration.
- When printing the edges of a book set using a single pattern, cover edges might become smudged in a series of books. This might also happen in the case of books with unlaminated covers.
- Where the book has an unlaminated cover, there is a risk of slight smudging of the cover edges.
- If the book block is warped or wavy, ink might seep into the inside through the gaps when printing on the edge.
4. Binding processes
4.1. Cutting of sheets
Permissible deviations when cutting sheets into individual pieces:
- Acceptable <= 1 mm
- Not acceptable > 1 mm
4.2. Folding and perforation
The deviation of the actual fold from the fold line results from preceding processes, i.e. cutting, and it does not usually exceed 1.5 mm. If – in addition to cutting and folding – a leaflet undergoes additional processes, such as die-cutting, the deviation from the fold line may increase up to 2 mm.
Permissible deviations for pages within a signature and for individual pages |
|
---|---|
for a 4-page signature without a crease | +/- 0.5 mm |
for a 4-page signature with a crease | +/- 1.0 mm |
for an 8-page signature | +/- 1.0 mm |
for a 12-page signature | +/- 1.5 mm |
for a 16-page signature (and larger) | +/- 2.0 mm |
4.3. Specific requirements for saddle-stitch binding
Features of a correctly-made saddle-stitch binding:
- the staples are not clenched too tightly, thus preventing the signatures from being torn inside the cover along the fold line,
- the number of staples used is consistent with the Client’s order,
- the staples keep the edges of the publication in line,
- the staple ends do not overlap.
In standard saddle stitch binding, the staples are placed at 1/4 of the height of the spine as measured from the footer to the header. The positioning of the staples should not shift either vertically or horizontally.
Permissible deviations in the finished product | ||
---|---|---|
Vertical positioning, flat staples | Vertical positioning, loop staples | |
Acceptable | <= 3 mm | <= 2 mm |
Not acceptable | > 3 mm | > 2 mm |
Where loop staples are used for binding, it is not acceptable for the positioning of the loop staples to shift to such an extent as to result in increasing or decreasing the distance between them and thus preventing them from being freely inserted into a ring binder. The standard loop size is 6 mm and the distance between them is 80 mm measured from the centre of the loops. The number, type and shape of the staples should be specified by the Client prior to commencement of the binding process.
4.4. Specific requirements for perfect binding
Perfect binding can be divided into two types of binding made using hot-melt and PUR technology:
- perfect binding (adhesive bound covers),
- sewn perfect binding (suggested for coated materials with a grammage of more than 115 g/m2).
The choice of binding depends on the intended use of the publication being bound. The minimum thickness of the spine is 2 mm and the maximum is 62 mm.
When choosing perfect binding, it should be remembered that in-line gluing of paper with low absorption properties (MWC, LWC), the adhesive may penetrate the book block. Such penetration cannot be completely eliminated without affecting the strength of the glued spine.
Perfect binding is considered correctly made if it is capable of withstanding a force of over 4.5 N/cm when tearing an individual sheet from the book. The durability of perfect binding can be verified through organoleptic evaluation. For binding to be considered properly made, its signatures (folded sheets) cannot fall out when the book is normally opened. In addition, binding is considered durable if – when the book is held by one of its middle pages and shaken gently – the page holds the weight of the entire book block and does not fall out.
Side gluing between the cover and the inside overlaps by a conventional 7 mm on each page (second page of the cover and first page of the inside, and last page of the inside and third page of the cover) and covers the image along the gluing line. If spreads are to be printed on those pages (images/graphic elements to be printed over more than one page), it is necessary to move them apart by 7 mm away from the spine (the image joint is then shifted by 7 mm). Internal spreads should also be moved away from the spine by 1.5 mm per page. It is possible for the glue to go over the crease set for the side gluing by up to 1 mm.
The durability of binding also depends on the grain direction. An incorrect alignment of fibres in the folded sheets inside the publication can result in cockling within the spine along the gluing line, which consequently makes the book difficult to open smoothly. An incorrect alignment of fibres in the folded sheets in relation to the cover (fibres running perpendicular to the spine) is often determined by the format of the project, a cost-effective layout of pages/pieces on the printed sheet and the print quality – at the same time, Totem cannot be held responsible for this.
The inside folded sheets should not be varnished on the spine as it will significantly weaken the durability of perfect binding; too big a difference between the grammage of the cover and the inside can cause the finished product to come apart.
Moreover, the format of the product to be bound and where the glue is applied also affect the durability of perfect binding (album format and the spine running along the shorter edge will significantly weaken the durability of perfect binding). This results from the ratio of the length of the edge to be glued to the length of the edge perpendicular to the edge glued.
It is possible for the glue and the ends of threads used to join the folded sheets in a block to protrude up to 1 mm beyond the crease provided to limit side gluing. Threads may be visible within the folded sheets and a very small amount of glue may be seen where the threads go through the spine of each signature. In the case of sewn perfect binding, there may be a slight lift of the spine along the cutting line, which is due to the difference in the thickness of the spine as compared to the rest of the bound surface.
Permissible deviations in the finished product:
Dimensional stability of the book
- Acceptable <= 1 mm
- Not acceptable > 1 mm
Shift in registration of the graphics on the spine of the book
- Acceptable <= 1,5 mm
- Not acceptable > 1,5 mm
UV/textured/raised varnish shift
- Acceptable <= 1 mm
- Not acceptable > 1 mm
Dry/metallic and colour foil embossing deviation
- Acceptable <= 1,5 mm
- Not acceptable > 1,5 mm
4.5. Specific requirements for hardcover binding
A hardcover book consists of a book block, to which the same standards apply as to perfect bound and thread sewn books, and a rigid protective cover (cardboard/covered base cases), the quality parameters for which are as stated below:
Permissible deviations in the finished product:
Cover format deviation
- Acceptable <= 1 mm
- Not acceptable > 1 mm
Deviation in positioning of the book block within the cover
- Acceptable <= 1 mm
- Not acceptable > 1 mm
Cardboard thickness deviation
- Acceptable <= 5 %
- Not acceptable > 5 %
Square size deviation
- Acceptable <= 1 mm
- Not acceptable > 1 mm
Shift in registration of the graphics on the spine of the book
- Acceptable <= 1,5 mm
- Not acceptable > 1,5 mm
UV/textured/raised varnish shift
- Acceptable <= 1 mm
- Not acceptable > 1 mm
Dry/metallic and colour foil embossing deviation
- Acceptable <= 1,5 mm
- Not acceptable > 1,5 mm
Additional deviations permitted in hardcover publications:
As regards colour embossing on textured materials, some colour deficiency on the printed surface is permitted (depending on the coating material used). The porosity of the cover depends on the quality and degree of smoothness of the surface of the smoothened cardboard. Since water-based adhesives are used in the binding process (joining of the book block with the cover), it is possible for cockling to occur on the book block and end papers. Hardcover binding can come with a flat or rounded spine. The quality and degree of rounding depend on the texture of the material used (type of paper), the number of pages in the book and the format of the project itself.
4.6. Format of the finished product
The format of the finished product is measured in two dimensions: from the spine to the front edge of the product – width, and from the top edge to the bottom edge of the product – height. The format of the finished product should meet the parameters specified by the Client.
Permissible deviations from the order as regards the format of the finished product:
- Acceptable <= 1 mm
- Not acceptable > 1 mm
The trimmed, perpendicular edges of the product should form a right angle (90°), the deviation from rectangularity is measured in relation to the spine and should never exceed 1,5 mm as measured along the longer edge of the item:
- Acceptable <= 1,5 mm
- Not acceptable > 1,5 mm
4.7. Additional components of the book
If any extra components are ordered (e.g. loose or glued inserts etc.), the materials should be described with a precise positioning in the project. Any notes should be confirmed by e-mail.
5. Discrepancy in the print run
The printing house reserves the right to certain tolerances regarding the number of the products actually delivered as compared to the quantities on the order.
Print run (no. of copies) Max. acceptable tolerance | |
---|---|
1-99 | 5% |
100-499 | 3% |
500-1,999 | 3% |
over 2,000 | 2% |
If an underrun or any defective copies are detected by Totem, where the number of copies does not exceed the tolerances shown in the table, complaints will not be accepted (unless otherwise agreed in a relevant contract with the Client). In the case of an underrun detected at the printing house, the Client will be notified prior to shipment and the invoice issued to the order will be automatically reduced accordingly.
6. Packaging and shipment
As a rule, the goods are packed in 5-layer corrugated cardboard boxes (double wall, EB flute, grammage: 618 g/m2).
Standard box formats:
- 400 mm x 280 mm x 400 mm
- 365 mm x 240 mm x 375 mm
- 303 mm x 216 mm x 360 mm
The date confirmed in the system by the Client is the date of shipment of the goods from the printing house, and the physical delivery of the product, depending on the destination, takes from 1 business day upwards:
- domestic shipments up to 200 kg – 1 business day,
- full-pallet domestic shipments – 2 business days,
- international shipments, subject to quantity and destination – between 2 and 5 business days.
In the event that the shipment is delivered damaged, the Client is required to fill in a shipping damage report and prepare photographic evidence in the presence of the forwarding agent. Complaints will be processed based on the report and photographs.