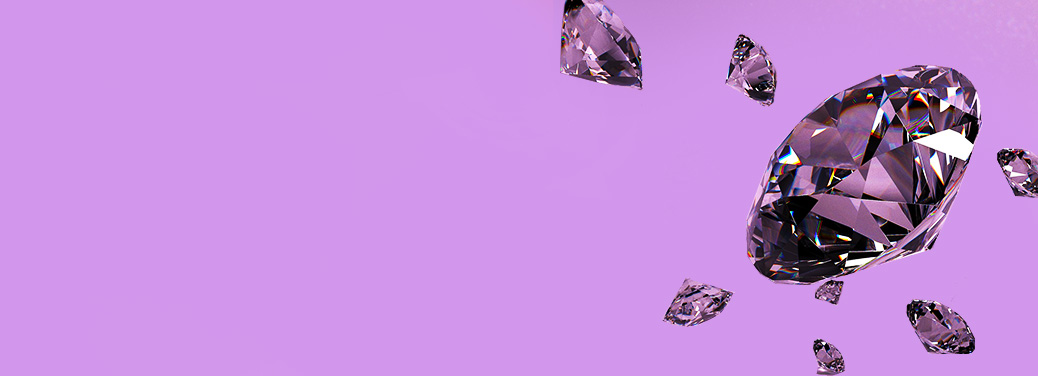
All about enhancements
Graphic designers often lose sleep over one particular comment made by clients: “the design is lovely, but there is no WOW effect." Admittedly, we are not able to cure all the ills of graphic designers, but when it comes to designing book covers, the WOW effect is at our fingertips. Enhancements applied to covers will make our publications stand out from the others on the bookshelf. We all know very well that you should not judge a book by its cover, but he who has never bought a book for purely aesthetic reasons, let him be the first to cast a stone.
Enhancements – what are they?
In the most general terms, print enhancements are treatments applied to printed surfaces using various techniques aimed at making the appearance of publications more attractive. Additionally, some of the treatments improve the publication’s durability, consequently expanding its lifespan. Enhancements are usually applied to sheets that have already been printed on, but before starting the different bookbinding processes. We have a whole range of enhancements available, however let us focus on the most popular ones.
1. Foil lamination
This is the basic and most often chosen type of enhancement. It entails coating the entire printed surface with transparent plastic foil. The foil means that the book cover is not only protected against moisture and mechanical damage, but it also looks better. There is a choice of several types of foil, the main difference between them being the effect we achieve on the laminated surface.
Glossy foil is by far the most resistant to scratches and external factors. To apply this type of foil we need to carefully consider what is to be printed on the cover – a compact block of text is not the best idea for purely practical reasons. Our eyes tire when trying to read texts printed on shiny surfaces, so if we want to encourage readers, there is no point in throwing up roadblocks for them to try to get over.
Matte foil has qualities similar to that of glossy lamination, while additionally giving us the peace of mind as to the legibility of the text. The matte finish means we obtain a sophisticated and elegant surface. Unfortunately, this kind of foil has some disadvantages too, namely the fact that it scratches easily. Sometimes even moving the publication across the surface of a table can result in new scratches. If we are dealing with a brightly coloured cover, these small imperfections are not too noticeable. However, for a dark cover we recommend applying anti-scratch matte foil to substantially reduce the chance of scratching our publication.
An interesting option (and our personal favourite) is soft-touch foil which is similar in appearance to the matte finish. Its unique qualities are revealed when we pick up a book covered with it – it is simply nice, even velvety to the touch. Obviously, there is a fly in this particular tub of ointment: dirty and oily fingers will leave marks on a cover with a soft-touch finish, but worry not – just wipe the cover down to make it clean again.
2. UV varnishes
This technique involves coating the printed surface with a varnish and then UV curing it.
Spot (UV) varnish (also referred to as selective coating) is a popular and relatively inexpensive type of enhancement. The varnish is only applied to a selective area on our cover – these can be strategic elements to highlight the graphic, e.g. author’s name, book title or a detail of an image. If, however, we want to approach the subject somewhat more creatively, we can forego the printed graphic in favour of just the varnish itself – the varnish will contrast with the surface of the cover left uncoated, thus creating something similar to a watermark. When experimenting like this, it is good to choose an uncomplicated shape, easy on the reader’s eyes. Glossy varnishes are without doubt most popular, however matte coating can also be used.
3D raised varnish works in a similar way, where the raised effect comes from the increased volume of the varnish achieved in the drying process. The result is a three-dimensional aspect to our publication, and the elements coated with this type of varnish are highlighted with added texture. When working with raised varnishes it is worth remembering not to apply them over too large of an area of print – the varnish can “collapse” in the middle, leaving us with an uneven finish.
When we want to go for something fancy, the answer is glitter varnish – a coating with glitter particles suspended in it. This type of varnish has as many opponents as it has advocates, with the former believing that the addition of glitter results in something bordering on kitsch, while the latter just know that – when used carefully and in moderation – glitter can add a bit of class to the publication, as befits enhancements.
The enhancements discussed above go well together with foil-laminated surfaces. As far as uncoated papers are concerned, foils are simply indispensable – offset papers tend to “soak up” the varnish, thus leading to a poor end result that is far from the effect desired by the designer.
3. Calendering
While deciphering the terms “lamination” and “varnishing” should not present a problem to anyone, “calendaring” may sound quite exotic. Calendering gives the printed surface the required texture, e.g. linen or leather. The printed surface is coated with foil and then passed between the rotating calender rollers. The pattern embossed on the rollers is consequently imparted on the foil-coated paper. Matte, glossy, soft-touch and structural foils can be used for calendering.
4. Dry embossing and hot-stamping
Hot-stamping is a particularly attractive enhancement. It introduces gold, silver and other glossy metallic shades to our design.
The process of hot-stamping requires three fixed elements – convex die, foil and (as the name suggests) high temperature. The die is made of heat-conductive material. The heated die transfers the foil onto the printed cover, with the adhesive on the foil becoming activated due to the high temperature. This results in the image carved on the die being imprinted on the printed surface. It is worth remembering that the price for this enhancement depends on the size of the die – the larger the die, the more foil will be used, and therefore the cost will be higher. However, looking at the effect achieved, sometimes hot-stamping is worth every penny spent…
Dry embossing (dry die)
Dry embossing gives us the opportunity to enhance our prints with 3D effects. It involves pressing our surface with a die (or a negative of a die, aka a counter die) in such a way as to permanently imprint the image carved on the die on the cover. The dry die can be used on both non-printed and printed surfaces – where it is aimed at raising the previously printed design (e.g. the title and the author’s name, the logo of the publishing house or a decorative element).
5. Die-cutting
A particularly eye-catching enhancement, and although it tends to be associated with publications for children, graphic designers successfully use it in books for adult readers. Die-cutting is neither the cheapest nor the simplest enhancement to design, so we truly hope that only seasoned book-printing designers will be taking on the challenge. The shape created by the designer is cut in the cover using a cutting die. What are the things to remember about? If we have a “gaping hole” in the cover, then inevitably – even when the cover is closed – we will always see the end paper. So let’s try and make it go with our hole: matching graphics, or even suitably laid out text (both have to look good also when the cover is open) will surely have a positive impact on the aesthetics of our publication.