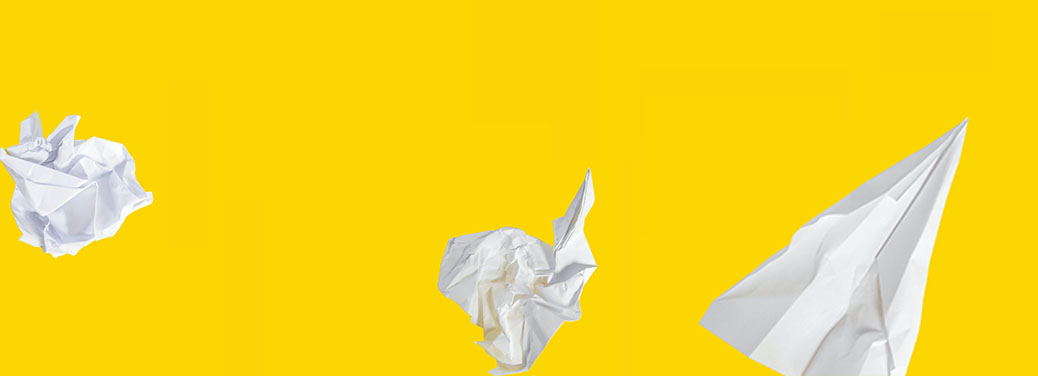
How is paper made?
The process of paper manufacturing is both fascinating and complicated. Unfortunately, we need some simplification and shortcuts to make it easier to understand how a tree trunk is turned into a liquid to become a bright sheet of paper. What sounds like magic is in fact a matter of technology.
Where does the wood come from?
From a forest, obviously. According to the State Forests, the wood that arrives at paper mills comes from tending operations. Young tree stands are thinned to provide more space for stronger trees to grow. The cut trees are transported to paper mills, where paper is made. However, for papermaking not the wood itself but its cellulose fibres are required.
Sourcing the fibres
Chemical method
In this method wood is first ground into chips which are then digested by chemicals. As a result the entire cellulose contained in the wood is preserved without any other undesired ingredients, so the pulp is called ‘wood-free’. By the way – you may have heard the term ‘wood-free paper’. This does not mean that wood was not used to produce it, but that apart from cellulose only very small quantities of other wood components can be contained in it. Fibres obtained using the chemical method are long and resistant to ageing.
What happens to the other components of pulpwood? After all, cellulose makes up less than half of its volume. What about the rest? Well, it is used either as a raw material or a source of energy. Thanks to that modern papermaking plants are often self-sustaining.
Mechanical method
In this method wood is ground until cellulose fibres are separated. Unlike in the case of the chemical method, not only cellulose but also other wood components, such as lignin and resins, are used for the production of paper. As a matter of fact 95 per cent of the pulpwood is utilized.
These two are not the only methods of sourcing the cellulose fibres. There are a number of others and some methods are combined, e.g. chemi-tehrmomechanical. We are not discussing them today though.
Paper stock
Paper is made from paper stock. The key question at this stage of the manufacturing process is to prepare the cellulose correctly, because this affects a few properties of the final product to be made from the stock. The fibres are ground to make them more flexible and plastic. However, the main ingredient of paper stock is not the fibres but water – as much as 99 per cent. Then there is usually some paper adhesive, carbon carbonate and dyes. When the stock is ready, it is transferred to a papermaking machine.
Papermaking machine
As the paper stock is essentially liquid, we can say that the main purpose of a papermaking machine is to remove the moisture. From the moment the stock is pumped into the machine until the paper is formed it undergoes repeated drying at different stages. If you have read our blog entry What is in paper?, even a finished sheet of paper is not completely dry. Depending on the type of paper it can contain 3-7% of water by weight.
Papermaking machines are impressively huge. They can reach a length of 150 m and can be 11 m wide. And the time needed to turn stock into paper is simply stunning: it takes 10-30 seconds! The speed at which paper web moves in the machine can exceed 2,000 m per minute.
The stock is poured into a head tank from which it is transferred onto a wire mesh. Here a great portion of water is removed by draining elements and vacuum. The next step is pressing by means of cylinders and felts, which dries the stock further. At this stage, such properties as rigidity, strength, opacity and volume of the paper are obtained. Next, the paper web goes through a series of steel cylinders and heated with steam. The pre-drying stage is very important, as it is here that the stock becomes dry enough to be called paper. Afterwards, surface sizing takes place. It involves coating the web surface with a thin layer of starch, which makes the paper more durable and resistant to abrasion, reduces dust and improves printing properties. Depending on the type of paper, the following stage can consist in friction pressing or calendaring, which gives the paper its final thickness. Then it is rolled onto a paper reel (tambor). The final stage involves cutting to sheets or smaller reels. Now the paper is ready for distribution.
In this form paper arrives at the printing shop, ready for printing on.